La Tecnologia Thermal Spraying
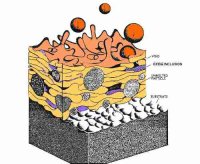
Nonostante le tecniche di spruzzatura termica (detta anche metallizzazione o riporto a freddo) esistano già da diversi decenni, la loro conoscenza a livello industriale, ma spesso anche universitario è ancora limitata. Per questa ragione ci è sembrato opportuno spendere due parole per dare una panoramica ai nostri clienti delle tecnologie da noi utilizzate.
In questo tipo di processi le polveri dei più svariati materiali vengono riscaldate e spruzzate da una fiamma che esce da una pistola sopra il pezzo che si desidera ricoprire. Le particelle, che si trovano in fase liquida o semi-liquida, si deformano nell’urto contro il substrato e si raffreddano di colpo. La gran quantità di dischi di materiale sovrapposto (splat) che si origina genera uno strato continuo e relativamente compatto.
Normalmente si separano le differenti tecniche di spruzzatura termica a seconda della fonte di generazione del calore: combustione, plasma o elettricità (più una quarta tecnologia chiamata cold spraying ancora piuttosto sperimentale). La grande ricerca in questo campo ha successivamente prodotto tutta una serie di sottocategorie che si differenziano per l’atmosfera di spruzzatura piuttosto che per le velocità di spruzzatura (vedi diagramma sotto).
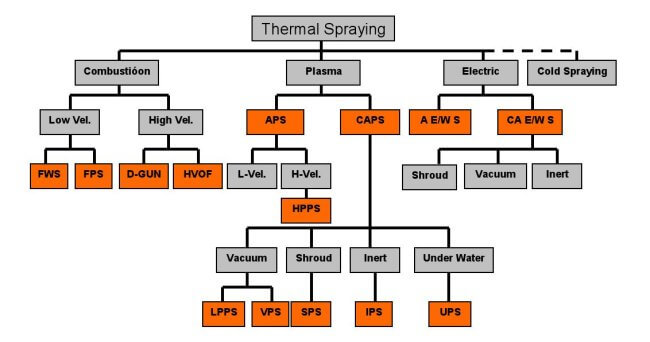
La Borgameccanica è in grado di realizzare rivestimenti metallici e ceramici adottando tutte le tecnologie più utilizzate di Thermal Spraying:
Low Velocity Flame Spraying
(detta anche Metallizzazione, o semplicemente Flame Spraying)
É il processo più semplice e più antico di spruzzatura termica. Il materiale di apporto entra direttamente nella camera di combustione sotto forma di filo (Flame Wire Spraying) o di polveri (Flame Powder Spraying). Il combustibile più utilizzato è l’acetilene, per l’elevata temperatura della fiamma che genera, tuttavia si possono utilizzare anche metano, idrogeno, propano, ecc. L’impianto è relativamente leggero e poco costoso però, a causa delle temperature e velocità delle polveri inferiori a quelle delle altre tecniche di spruzzatura termica, i rivestimenti sono più porosi, meno densi e meno aderenti al substrato. I materiali normalmente spruzzati sono metalli e leghe con bassa temperatura di fusione, o polimeri.
HVOF
(High Velocity Oxy-Fuel Spraying)
Si tratta di una categoria di processi che deriva direttamente dalla LVFS. Le polveri introdotte nella camera di combustione si riscaldano e accelerano fino a raggiungere velocità molto superiori a quella del suono, attorno ai 700 ms-1. Le elevate velocità di spruzzatura del materiale e le temperature piuttosto basse sono caratteristiche fondamentali di questa tecnica, che consente di ottenere rivestimenti molto compatti. Nonostante sia relativamente recente questa tecnica è in grossa crescita anche perchè consente di ottenere rivestimenti in grado di sostituire la cromatura elettrolitica in molte applicazioni.
Plasma Spraying
In un processo di Plasma Spraying un gas inerte, solitamente argon, passa per un anodo convergente-divergente di rame raffreddato con acqua. La corrente continua applicata fra questo anodo e un catodo, normalmente fatto di tungsteno, provoca la formazione di un arco elettrico che riscalda e ionizza il gas. Le temperature del fascio di plasma e delle polveri proiettate sono notevolmente superiori di quelle dei processi di combustione, però le velocità di spruzzatura non sono così elevate. Per questa ragione con questa tecnica si spruzzano anche materiali con elevata temperatura di fusione, come ceramici quali Al2O3, Cr2O3 y ZrO2.
Materiali Spruzzabili
I materiali spruzzabili con tali tecnologie sono davvero innumerevoli. A continuazione vengono elencati solamente i rivestimenti maggiormente utilizzati:
- Acciaio Inox. In tutte le applicazioni che richiedono l’utilizzo di acciai inox è spesso possibile rivestire solamente la superficie del pezzo e realizzarlo perciò in materiale meno pregiato e costoso.
- Leghe base Nichel. Rivestimento metallico con una durezza elevata e buona resistenza alla corrosione, resiste alle alte temperature (fino a 800°C) e presenta un basso coefficiente di attrito.
- Leghe base Cobalto. Per molti aspetti sono simili ai rivestimenti base nichel ma forniscono maggiore resistenza alla corrosione.
- Ossido di Cromo. Molto utilizzato in ambienti corrosivi e per la grande resistenza ad usura.
- Ossido di Alluminio (Allumina). Si adotta in campo alimentare e per realizzare barriere ed isolamenti elettrici.
- Ossido di Zirconio (Zirconia). Grande resistenza alle elevate temperature, viene adoperato per realizzare barriere termiche.
- Cermet Carburo di Tungsteno-Cobalto WC-Co-(Cr). Negli ultimi anni questo materiale composito sta prendendo rapidamente piede per la sua eccezionale durezza e buona tenacità.
Non esitate a contattarci, saremo lieti di aiutarvi a trovare la risposta alle vostre problematiche produttive.
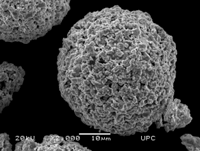
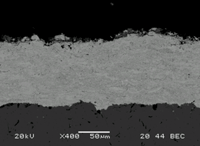
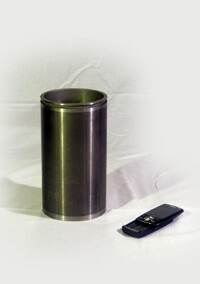